Strike force: the making of Will Yates-Johnson and NasonMoretti’s matches vessels
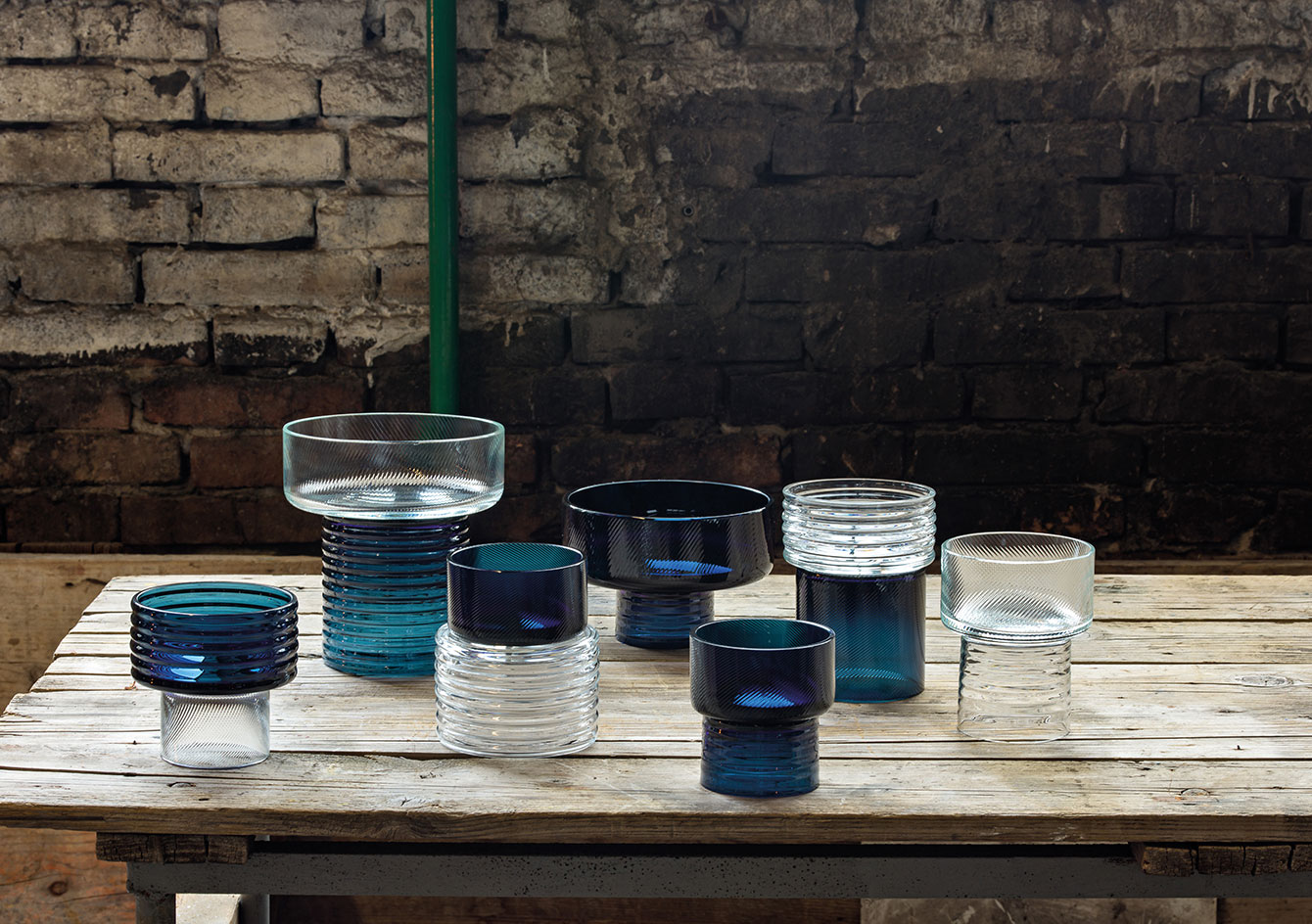
The Calle Dietro Gli Orti, which takes you to the gates of NasonMoretti’s glass factory, is a crazy-paving footpath that passes quaint homes and doubles as the entrance to a Nason family-owned B&B located in a 16th century palace. The factory is on the island of Murano, just north of Venice, and there are no roads. But that’s OK as the glass factory has its own landing dock on Canale Serenella.
‘Everything is on a grand scale and is incredibly beautiful, it’s right on the water’s edge,’ says London-based designer Will Yates-Johnson. He travelled to Murano earlier this year to oversee the production of a series of glass vessels that would hold our specially commissioned Hotel Wallpaper* matches.
The Nason family has been making glass on Murano since the 1920s. Now in its third generation, it is still operated by four cousins, descendants of Umberto Nason, who brought the company awards and international renown in the 1950s and whose modernist designs are in the collection of MoMA.
Travelling to the factory was crucial for Yates-Johnson to be able to understand the factory’s hand-blowing techniques and explore its archive of moulds and colours. ‘One of our specialisms is the technique of rigadin ritorto,’ says Marco Nason. ‘Delicate lines are created in the glass by using two moulds: the first mould makes the lines, while in the second, the master-blower will twist the glass to angle the lines. We have perfected the technique over the past 50 years.’
What interested RCA graduate Will Yates-Johnson, who created the striking, sculptural lettering for the cover of our 2016 Graduate Directory issue, was the combination of a handmade technique and the regularity of mould-blown glass. ‘The glass that these techniques produce appears to be quite mechanical and quite automated. They seem less handmade than a lot of other techniques that Murano glassmakers specialise in. You often see Murano glassware that emphasises its “handmadeness”, things will be a bit wobbly and unique. What I loved about these techniques is that they almost fool you into thinking, “Is this machine or human made?” and I like that ambiguity.’
The final form was created by fusing two separately blown pieces – the delicately lined rigadin ritorto pieces and the glass made using a corrugated mould that Yates-Johnson found in the factory’s archive. ‘They really keep stuff. This mould was created in 1968 and had been gathering dust for decades. It had fallen out of use because customers thought it looked too industrially produced. Much of my work is about finding new angles on existing things so it was perfect.’ The mould also helped create rounded forms that echoed the cylindrical shape of the matchboxes created for Hotel Wallpaper*.
The colour of the vessels, taken from the archive and called ‘Aviation Blue’, was chosen because it was a close match to our brand hue – the ‘Wallpaper* Blue’ developed by our creative director Sarah Douglas and British paper company James Cropper. The colour was used in the compositions intermittently, alongside clear glass, to complement the matchboxes.
Coloured glass, a Murano speciality, is created by dry mixing minerals, oxides and chemicals in specific quantities. Blues require some copper and cobalt compounds, but the exact finish depends heavily on years of experience in understanding how the additives interact. ‘So much of what they do in the factory is a function of generations of expertise,’ says Yates-Johnson. ‘Their artistry is about knowing the materials; knowing its properties; knowing what you can and cannot do with it. The master glass blowers have been doing it since their apprenticeships, and now most of them are in their fifties and sixties. It really isn’t something you can teach yourself.
As originally featured in the August 2016 issue of Wallpaper* (W*209)
See more from Handmade here and check in to Hotel Wallpaper*…
Yates-Johnson embraced NasonMoretti's expertise in a process called rigadin ritorto, where molten glass is poured into a ribbed bronze mould, to create the fine lines in the vessels
The ribbed bronze moulds used in the rigadin ritorto process
The final form of the vessels is created by fusing two separately blown pieces together
INFORMATION
Available at WallpaperSTORE*. For more information, visit Will Yates-Johnson's website and the NasonMoretti website
Photography: Matteo Piazza
Receive our daily digest of inspiration, escapism and design stories from around the world direct to your inbox.
-
Nipa Doshi's multidimensional cabinet nourishes mind, body and soul
Nipa Doshi is the Recipient of the 2025 Mecca x NGV Women in Design Commission; in Melbourne, she creates a miniature world that blends cultural heritage and personal memory
-
Meet the landscape studio reviving the eco-brutalist Barbican Conservatory
London-based Harris Bugg Studio is working on refreshing the Barbican Conservatory as part of the brutalist icon's ongoing renewal; we meet the landscape designers to find out more
-
‘A Single Man’ is now a ballet – we go behind the design
As ‘A Single Man’ is presented by The Royal Ballet and Factory International in London, here’s how its set designer brought protagonist George’s inner and outer worlds to life on stage
-
The Macbeth, an icon of indie sleaze, goes from grotty to gastro
An East End legend meets Portuguese small plates in Jamie Allan’s ambitious revival of a beloved Hackney watering hole
-
A complete collection of Phaidon’s ‘Contemporary Artists Series’ is on display in London
A 30-year project reaching 100 volumes is being celebrated with an exhibition at the 45 Park Lane hotel, including limited-edition works by Kaws and Dana Schutz
-
London’s best pizza restaurant gets a new home in Mayfair
Secure a slice of New York-style pizza in central London as Crisp Pizza teams up with the Devonshire pub to set up shop in the relaunched The Marlborough
-
Harry Nuriev’s Noisy Oyster London bistro isn’t quite finished – and that’s the point
A futuristic, work-in-progress aesthetic forms a striking backdrop for a new, sustainably focused seafood bistro in Shoreditch
-
Head to Lupa for a taste of Rome in the heart of Highbury
Ed Templeton, Theo James and Naz Hassan unveil an intimate 28-seat restaurant that balances a cosy, candlelit atmosphere with Roman-style dining
-
Underground grooves and a touch of ‘controlled chaos’ make this exciting Japanese-inspired restaurant one to book
Moi, a new subterranean hotspot in London, is a feast for the senses
-
Café Kitsuné doubles down on London with a new location
Café Kitsuné continues its global expansion with a bijou two-floor venue in Covent Garden that prioritises both craft and flavour
-
You can live out your Gatsby dreams, thanks to Claridge’s new Jazz Age-themed sleepover
Check in for the legendary hotel's Bright Young Things Sleepover — Shalimar perfume included