Tonkin Liu and ThusThat reimagine red mud
Red mud, a problematic waste product of aluminium turns planet-friendlier resource in the hands of designers ThusThat and architects Tonkin Liu
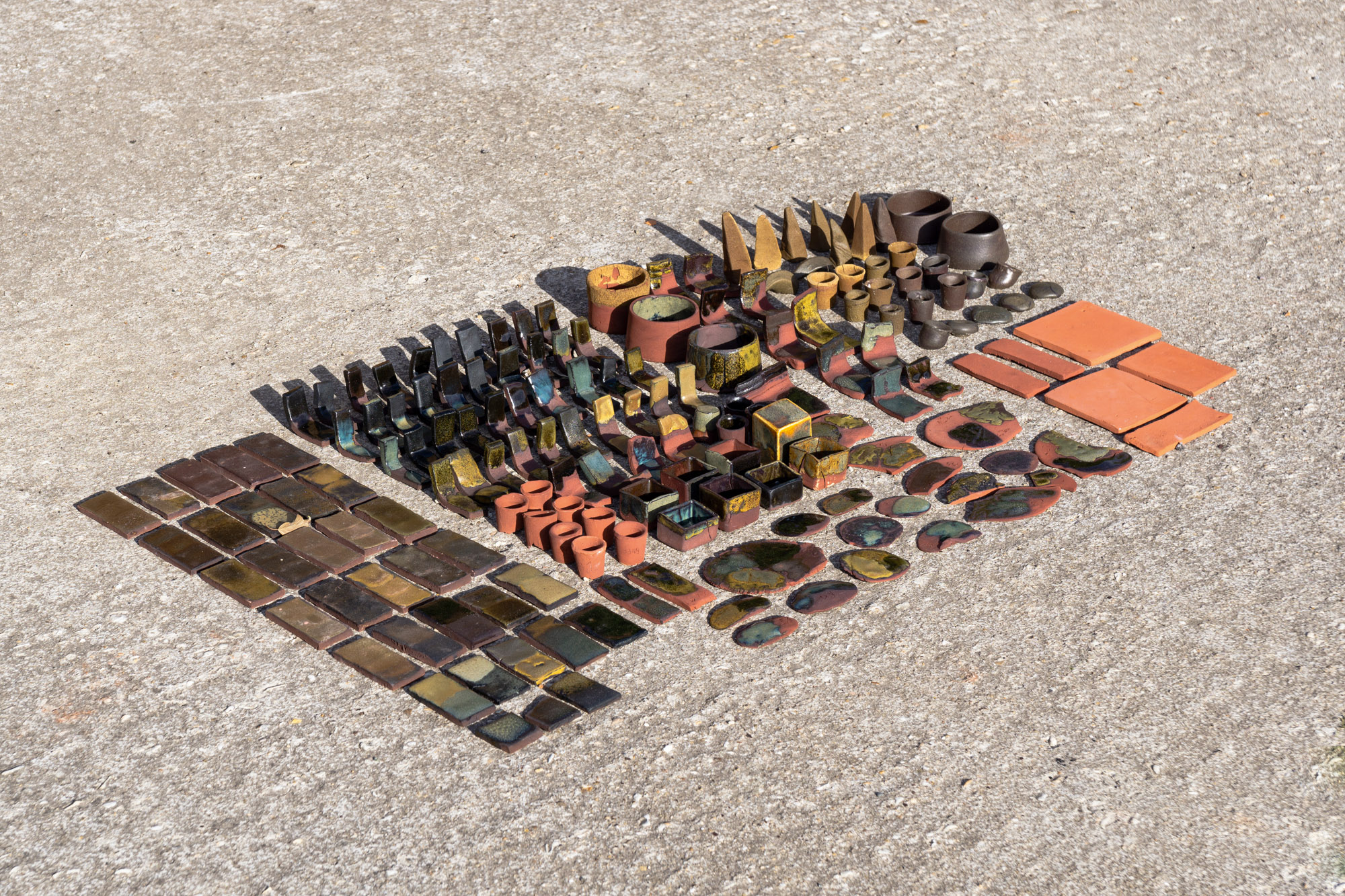
Imagine a world where manufacturing is so efficient that waste products become coveted, sustainable material resources. UK-based design group ThusThat is exploring just this reality with its research into ‘red mud’ – a by-product of the aluminium production process. The studio’s Kevin Rouff and Luis Paco Böckelmann have been studying this curious and previously fairly neglected by-product of industry. ‘To make aluminium, alumina needs to be extracted from bauxite ore. The residue of this refining process is red mud, also known as bauxite residue,’ says Rouff. ‘Decades of research are now coalescing, perhaps due to the rise of material consciousness. The gargantuan amount of red mud in landfill is beginning to be seen as an abundant material resource.’
Red mud has been around since the late 19th century, when Carl Josef Bayer discovered the alumina-extraction process, and Bayer himself suggested ways of using this waste. But 130 years later, ‘only about three per cent of it is being put to use, and mostly as road filler’, says Böckelmann. There has been little economic incentive to find an afterlife for red mud; particularly as it is classified as a hazardous material. Accidents involving the material have given it a bad name, although advances have been made in its safe handling and treatment. Rouff and Böckelmann suggest reducing the risk around it is crucial and possible.
Enter Tonkin Liu, the dynamic London architecture studio with a reputation for bringing together solid, rigorous research, a beautiful, ethereal aesthetic and clean, modern, yet often organically inspired shapes. Principals Anna Liu and Mike Tonkin have spent years developing approaches and techniques for efficient and effective architectural designs.
A Google Earth image reveals vast red mud pits alongside an aluminium plant in Australia, containing some of the 150 million tonnes of the waste material that is thought to be generated each year
Their ‘Shell Lace Structure’ method, a sort of reverse engineering of the biomechanics of mollusc shells, has been over ten years in development. Working with structural engineers from Arup, and using digital modelling, the pair worked out how to twist, fold, curve and perforate thin steel sheets to create light but incredibly strong and organic-looking spans, beams and pillars. When they heard of red mud’s potential, they jumped at the opportunity to experiment.
‘Given the limited resources in our world, all waste materials should be regarded as valuable materials, simply in the wrong shape and state, waiting for our imagination to transform them,’ says Liu. ‘This seems to sum up the spirit of Wallpaper* Re-Made,’ he adds, referring to the August 2020 issue of Wallpaper*, where this project was first featured, and which kicked off our ongoing focus on ‘Design for a Better World’.
The pair did their research. ‘There are two distinct characteristics [of red mud],’ continues Liu, ‘its vast quantity, and its journey in the global landscape, where it is mined, processed, stored, and was in the past discharged into rivers, estuaries or the sea. We decided to home in on its intriguing relationship with water.’ The sea, it turns out, can offer a safe route for handling and using red mud, as the water neutralises its alkalinity – it just needs to be done in the right way so as not to disturb aquatic life.
Tonkin Liu used its understanding of geometry and structure to come up with a new application for the material. The result? A tile-like product with numerous uses: for the creation of garden water features; as a roofing material; and to build an environment for plants and wildlife as part of coastal bioremediation. The design is scalable and modular. Each tile is profiled and they can be joined together to hold water and habitat or let planting push through.
Receive our daily digest of inspiration, escapism and design stories from around the world direct to your inbox.
Tonkin Liu’s ideas for using red mud tiles of various geometries and on various scales to regenerate waterside areas and for garden features
The architects got together with ThusThat for a series of brainstorming sessions, following their usual design methodology of exploration and experimentation. ThusThat’s expert knowledge of the material has been crucial in identifying challenges ahead. ‘We need to understand the economy of scale,’ says Tonkin. ‘At the moment, we are aspiring to collaborate with ThusThat to develop not just another commodity for consumers, but something that tells red mud’s compelling story in the landscape.’
Red mud can be sourced from various places, from factories to research facilities. ThusThat has been working on two main paths of treating the material. First the team soak, wash and sieve it to remove unwanted matter. They then run tests to understand the product’s ability to sinter as a ceramic, the highest temperature it will withstand, and its workability. From there, it can be treated like ceramic – processed like a traditional clay, formed or cast, and finally fired in kilns. But it can also work a bit like cast concrete, or geopolymers, where the technique is reversed by first firing the material, then working it mechanically, activating it, and casting it. For the Re-Made project, the collaborators are exploring both routes and are now seeking manufacturing partners to help bring the results to life.
‘We’d ideally like to develop something that could make use of large quantities of red mud, alleviating the environmental burden of storing it in vast vats in the landscape,’ says Liu. ‘Having worked on research projects in coastal towns in the UK, we are aware of issues of rising sea levels, and seaside towns in need of greening and regeneration.’ Coastal revitalisation is dear to the architects’ hearts, but there are other exciting possibilities.
‘Ultimately, red mud will likely be used in large-scale applications of the construction and architectural sector,’ says Böckelmann. ‘But a material’s narrative takes a long time to develop; cement has been in use since Ancient Rome, but it took nearly two millennia before it was modified to the ubiquitous form we know today.’ To develop red mud, he says, ‘we need to create the pull, and designers and architects are key to this. Projects such as this collaboration are important to demonstrate the possibilities in form, function and aesthetics.’
INFORMATION
Ellie Stathaki is the Architecture & Environment Director at Wallpaper*. She trained as an architect at the Aristotle University of Thessaloniki in Greece and studied architectural history at the Bartlett in London. Now an established journalist, she has been a member of the Wallpaper* team since 2006, visiting buildings across the globe and interviewing leading architects such as Tadao Ando and Rem Koolhaas. Ellie has also taken part in judging panels, moderated events, curated shows and contributed in books, such as The Contemporary House (Thames & Hudson, 2018), Glenn Sestig Architecture Diary (2020) and House London (2022).
-
Four under-the-radar travel destinations to book in 2026 – before everyone else does
You'd be forgiven if none of these locations are on your travel bingo card – yet
-
Estudio Ome on how the goal of its landscapes ‘is to provoke, even through a subtle detail, an experience’
The Mexico City-based practice explores landscape architecture in Mexico, France and beyond, seeking to unite ‘art and ecology’
-
Charlotte Chesnais brings her distinctive sensuality to sculptural new jewellery
Defined by curving shapes and luscious pearls, the jewellery designer's new collection, 'Joaillerie', has sculptural allure
-
What are biomaterials? Everything you need to know about Mother Nature's building blocks
Could the cities of the future be grown from plants, bacteria and fungi? Architects explain
-
What is eco-brutalism? Inside the green monoliths of the movement
The juxtaposition of stark concrete and tumbling greenery is eminently Instagrammable, but how does this architectural movement address the sustainability issues associated with brutalism?
-
Explore wood architecture, Paris' new timber tower and how to make sustainable construction look ‘iconic’
A new timber tower brings wood architecture into sharp focus in Paris and highlights ways to craft buildings that are both sustainable and look great: we spoke to project architects LAN, and explore the genre through further examples
-
Building with bamboo: In Bali, designer, Elora Hardy, shares her tips and experience
Bamboo architecture can be powerful and sustainable; here, we talk to Ibuku's Elora Hardy, who shares her tips, thoughts and experience in working with the material in Bali
-
Hermitage Mews is a net-zero family of homes in London’s Crystal Palace
Hermitage Mews by Gbolade Design Studio is a sustainable residential complex in south London's Crystal Palace, conceived to be green and contextual
-
Sustainable architecture: 46 innovative and inspiring building designs
This is sustainable architecture at its best: from amazing abodes to centres of care and hard-working offices, these buildings not only look good but also do good
-
Slot House sets a high bar for sustainable architecture in Utah
Slot House, an energy-efficient mountain retreat in Utah, by local practice Klima Architecture, sets the bar high
-
Spruce house offers a minimalist take on sustainable architecture
Spruce House, London practice Ao-ft’s debut project, is a carefully crafted timber house that perfectly slots into its urban landscape