Gold standard: creating Fabergé’s modern treasures
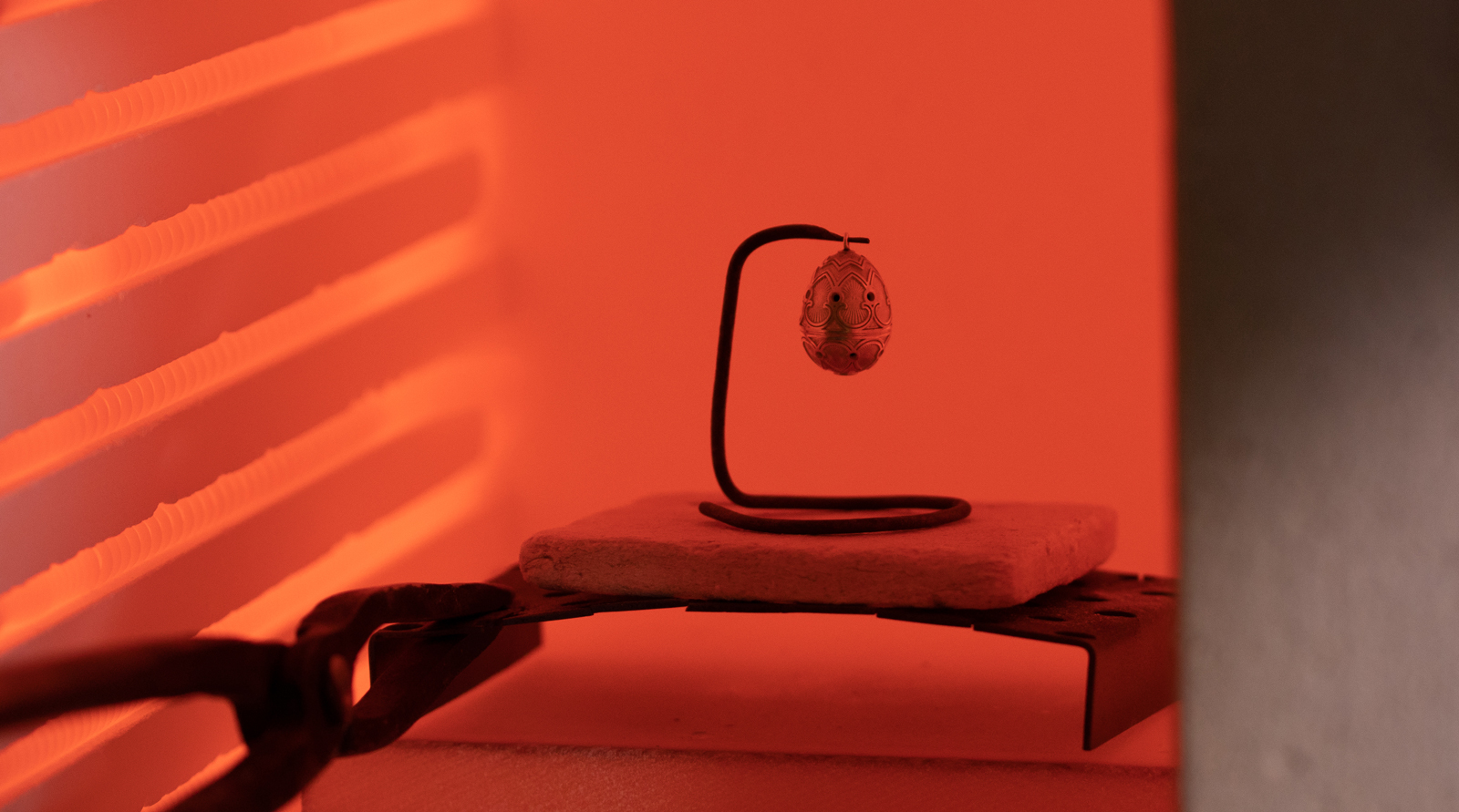
Of all the decorative crafts, enamelling is, and always has been, one of the toughest to master. Which is exactly why Carl Fabergé was so attracted to it. The outmoded enamelled guilloché techniques of 18th century French craftsmen Fabergé had come upon in museums during his European Grand Tour of the 1860s inspired the master goldsmith to revive them.
He also saw the potential for producing a spectrum of rich, glossy colours and tasked his workshops with developing a Fabergé palette. One hundred and forty-five shades were created, including the sugared-almond-like lilacs, pinks and yellows that denote the Fabergé style. The house further amazed its peers in its mastery of ‘in the round’ or – en ronde bosse – enamelling, which was crucial to its egg designs. The curves made it torturously difficult to achieve consistency in the liquified glass during firing in impossibly hot kilns.
Fabergé employs British-based jewellers and enamel artists to create traditional guilloché patterns in gold
Today, without the patronage of the kings and tsars that Carl Fabergé served, and with many traditional techniques now obsolete, it is not possible for a craftsman to spend a year embellishing one object, such as a Fabergé egg, to the impossibly exquisite level achieved by his 19th century St Petersburg workshops, and which continues to make original Fabergé pieces so awe-inspiring. But guilloché enamelling is still a mainstay of Fabergé, with elements appearing in the house’s contemporary jewellery, egg and watch designs.
Now, Fabergé employs British-based jewellers and enamel artists to create traditional guilloché patterns in gold. Egg pendants are hand-engraved, so that the enamel – powdered glass in tones reminiscent of the original Fabergé palette – can be applied. When a design is placed in a high-temperature kiln, the enamel fuses with the metal beneath. These layers of opaque colour highlight the swirled patterns of the gold, creating the illusion of shimmering, opalescent waves of light.
Guilloché metal patterns were typically created using a lathe. Fabergé craftsmen engrave them in gold by hand
Three egg parts in various stages of polish. The piece to the right is complete. After a lengthy firing and polishing process, its desired rich, glossy colour has been achieved
An almost complete Fabergé egg at the British enameller workshop
INFORMATION
ADDRESS
faberge.com
Receive our daily digest of inspiration, escapism and design stories from around the world direct to your inbox.
Caragh McKay is a contributing editor at Wallpaper* and was watches & jewellery director at the magazine between 2011 and 2019. Caragh’s current remit is cross-cultural and her recent stories include the curious tale of how Muhammad Ali met his poetic match in Robert Burns and how a Martin Scorsese Martin film revived a forgotten Osage art.
-
How architects are redefining disaster relief through design
Disaster relief architecture is a critical component of humanitarian aid across the globe; read our ultimate guide on how architects can make a difference through design
-
Paul Gulati on storytelling, multi-sensory design and the evolution of Universal Design Studio
'f a space works – not just as a beautiful image, but for the people using it – then we’ve done our job,' he tells us
-
Seiko and Datsun mark a shared heritage and history with three new limited-edition watches
The Japanese brands pay tribute to the Datsun 240Z and Prospex Speedtimer in a new collaboration
-
All eyes on Greek jewellery brand Lito as it launches bold new amulets to mark its 25 years
Striking amulets, seductive stones and secret messages characterise Lito's striking new anniversary collection, an extension of its ‘Tu es Partout’ series
-
The best layering necklaces for an elevated yet casual look
How to mix, match and stack jewellery for the ultimate high-energy, low-effort style
-
Art takes London: Tiffany & Co, Damien Hirst and artists take over Selfridges' windows
Four British contemporary artists celebrate Tiffany & Co's pioneering history with a series of storied window displays
-
Late summer jewels: what to wear at Golden Hour
Late summer signals a jewellery style-shift. These independent designers have got it covered
-
Emerging jewellery designers to get to know
These independent, new and emerging jewellery designers and brands from New York to Paris are firmly on our radar
-
Jewellery designers share their most precious personal pieces
A host of jewellers give us a peek at the jewellery which brings them joy and solace
-
Playing it cool: pearls are having a moment
We've been deep-diving into boutiques around the world to find the very best calcium carbonate in minute crystalline form. It seems jewellers have been busy rethinking pearls, with contemporary (and often affordable) results
-
Eternity rings for the modern couple
Eternity rings, whether sleekly minimalist or sprinkled in diamonds, can be a chic and contemporary love token