Spring board: Kvadrat, Really and Max Lamb set a new benchmark in sustainable design
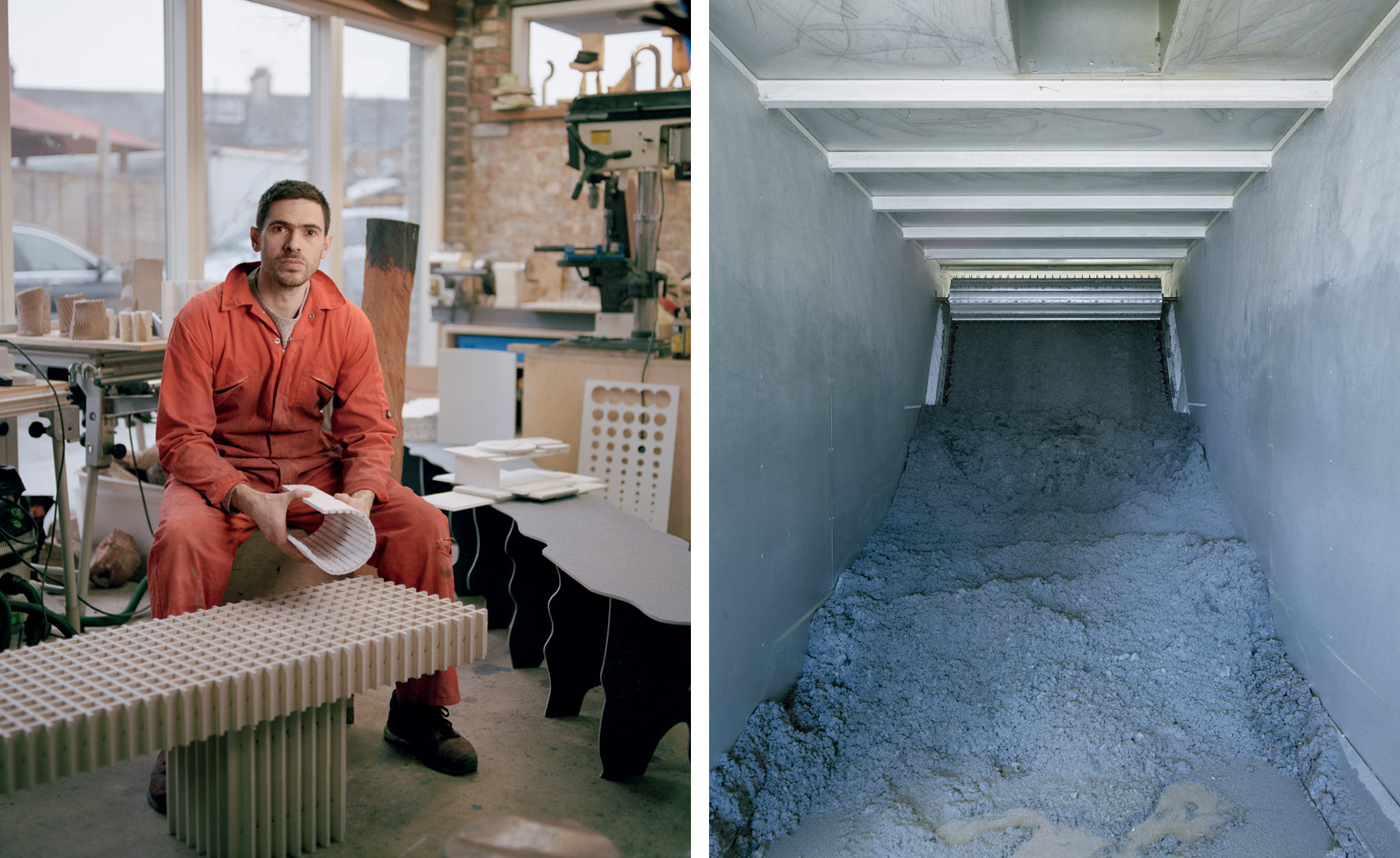
‘The design community has always been progressive, pioneering,’ says Kvadrat CEO Anders Byriel. ‘I think we forget how much impact it has – creating the products we all use and our surroundings. It can change the world.’ With that mission in mind, Kvadrat is coming to Salone del Mobile with a new material it hopes will prove a breakthrough for sustainable design. The textile giant has partnered with Really, a Danish start-up producing Solid Textile Board – a material made using recycled ‘end-of-life’ fabrics, mostly cotton and wool. The board is a first in the industry, and Kvadrat and Really have enlisted designer Max Lamb to create a collection that expresses its potential.
Long passionate about sustainability and recycling, Byriel now heads up the company his father co-founded in 1968; and these passions inform his decisions. ‘At Kvadrat we have always been obsessed with sustainability, and our audience is into it, too,’ he says. ‘As a business, you need to be progressive, move out of your safety zone, move faster.’ At Kvadrat, the aim is to reduce environmental impact in terms of resources, production and distribution, and to balance quality, social responsibility and environmental concern. It was such concerns that first attracted Really co-founder Wickie Meier to Kvadrat. Meier, who has taught sustainability in fashion at Esmod Berlin since 2011, had launched Really in 2012 in collaboration with Klaus Samsøe, co-founder of fashion label Samsøe & Samsøe and a pioneer of Danish fashion and recycling. Their ambition was simple: to give new life to end-of-life textiles.
Production of felt mats from the fibres.
Samsøe had learned that in Denmark alone, 1,000 tonnes of textiles is thrown away each year and incinerated. This is mostly cotton waste from the hospitality industry, but also denim and wool. Samsøe and Meier started thinking about how they could do something more with the waste than simply recycle it in its textile form. They wanted it to work on an industrial scale and landed on the Solid Textile Board idea.
The process behind the Really boards is simple and the technology it employs is not new. Samsøe and Meier simply devised new ways to use it. The raw material comes from different sources: cotton from Danish industrial steam laundries and a large Italian fabric recycler, as well as leftover wool from Kvadrat. The textiles are granulated into smaller fibres and ‘airlaid’ using steam machinery – a process that binds the short fibres – then flat-pressed to become hard board. No water or dye is used in the process and each board is produced in a standard size with a white, dense core made of cotton fibres and top layers that can be achieved using cotton or wool. The boards are available in white, blue or slate, depending on the material used. At the moment, they are being produced in a converted barn in Ebeltoft, near Kvadrat HQ, but Meier and Samsøe insist that production could be adapted to any location in the world.
‘This is a really serious material,’ says Lamb. ‘These raw materials haven’t been put together in this way before. It has amazing potential and properties, and therefore implications within the industry.’ Both Meier and Byriel say Lamb was the natural choice to help launch Solid Textile Board. He has a history of radical thinking with raw materials, including a dissected tree (from his grandfather’s garden), which he turned into furniture with minimal interventions on the trunk, and a series of polystyrene chairs titled ‘Scrap Poly Pastel’. ‘Each material has its own set of possibilities,’ says Lamb. ‘My work is about trying to extract the best of a material, in the simplest way; it’s about how little I can do to it to achieve the most.’
A stack of felt mats ready for pressing to create the solid textile board.
Having been involved with Really on the development of Solid Textile Board for over a year, Lamb got to grips with its composition and potential; experimenting with it back at his London studio allowed him to understand what he calls ‘the material’s personality’. One important feature, he notes, is the nondirectional composition of the fibres, which renders the board more flexible than other examples on the market.
Lamb chose the bench as the ideal piece of furniture to explore the material’s versatility, and produced 12 different designs that investigate its full potential. ‘The bench is a medium that really shows off the board. And also a bench is to be sat upon, and I want many people to sit on it, and become physical and intimate with the material,’ he says. The designer also stresses that almost every inch of the material was used, but that the Really system allows any offcuts to be recycled and incorporated into new boards.
Each bench will make use of the board’s 3.1m length, and their shapes are achieved using a variety of techniques: Lamb layered boards or cut them and slotted the pieces into each other, shaped them using different CNC cutting techniques, bent them to exploit the flexibility of the material, applied V-cuts and folded them into boxes for extra stability.
Cutting the board.
‘We thought that Max could release the materiality of Really,’ says Byriel. Meier agrees: ‘His contribution is not about seeing the object, it’s about seeing the potential,’ she adds. For her, intelligent design is essential to convey Really’s sustainability message. ‘Design is communicating, it’s problemsolving, it brings interaction,’ says Meier. But in the long run, it also has to help us make things more sustainable. ‘Design is needed to bring sustainability to that convenience level that we need to achieve to get things moving.’
Curated by Jane Withers, the Milan presentation will be accompanied by a book edited by Christien Meindertsma, offering an in-depth look at Solid Textile Board and Really’s role in its development. The brand’s name is a result of the process, and of Meier and Samsøe’s incredulity at seeing the board become a reality. ‘We were looking for a name that sounded happy: when you work with sustainability everything can be very serious,’ explains Meier. ‘And then we realised we kept saying that word: “Is this really happening? Are we really doing this?”’ They did, Really.
The Really factory in Ebeltoft, Denmark, where the sustainable hard board is produced.
Anders Byriel and Wickie Meier with bags containing fibres used to create the board.
Lamb's collection was exhibited at ProjectB Gallery during Milan Design Week
Installation view of 'Really: Designing Materials for Circularity' at ProjectB Gallery
Two of Lamb's benches illustrating the flexibility of the material.
INFORMATION
‘Really: Designing Materials for Circularity’ ran from 3 –9 April at ProjectB Gallery in Milan. For more information, visit the Kvadrat website and Max Lamb’s website
Receive our daily digest of inspiration, escapism and design stories from around the world direct to your inbox.
Rosa Bertoli was born in Udine, Italy, and now lives in London. Since 2014, she has been the Design Editor of Wallpaper*, where she oversees design content for the print and online editions, as well as special editorial projects. Through her role at Wallpaper*, she has written extensively about all areas of design. Rosa has been speaker and moderator for various design talks and conferences including London Craft Week, Maison & Objet, The Italian Cultural Institute (London), Clippings, Zaha Hadid Design, Kartell and Frieze Art Fair. Rosa has been on judging panels for the Chart Architecture Award, the Dutch Design Awards and the DesignGuild Marks. She has written for numerous English and Italian language publications, and worked as a content and communication consultant for fashion and design brands.
-
Estudio Ome on how the goal of its landscapes ‘is to provoke, even through a subtle detail, an experience’
The Mexico City-based practice explores landscape architecture in Mexico, France and beyond, seeking to unite ‘art and ecology’
-
Charlotte Chesnais brings her distinctive sensuality to sculptural new jewellery
Defined by curving shapes and luscious pearls, the jewellery designer's new collection, 'Joaillerie', has sculptural allure
-
Seven Studio lends a modern, gritty edge to traditional Mallorcan stone carving
Founded by an artist-and-art-director duo, Seven Studio crafts furniture and objects that blend timeless beauty with bold brutalism
-
O Milano! Design's epic annual spectacle in photos
Call us biased, but we believe that Milan Design Week is, at this moment in time, the greatest show on earth
-
‘Romantic brutalism’ rethinks Polish craft
An exhibition in Warsaw gives local makers their due, looking inside the burgeoning world of Polish design
-
Eight designers to know from Rossana Orlandi Gallery’s Milan Design Week 2025 exhibition
Wallpaper’s highlights from the mega-exhibition at Rossana Orlandi Gallery include some of the most compelling names in design today
-
Bentley’s new home collections bring the ‘potency’ of its cars to Milan Design Week
New furniture, accessories and picnic pieces from Bentley Home take cues from the bold lines and smooth curves of Bentley Motors
-
StoneX partners with Wallpaper* for material alchemy at Milan Design Week and beyond
The natural stone purveyor teams up with Wallpaper* for a three-year partnership of material adventures, starting with an exhibition at Triennale di Milano
-
David Rockwell’s Milan Design Week presentation is a love letter to cork
Rockwell Group’s Casa Cork installation showcases this under-appreciated material, which is infinitely recyclable and sequesters carbon for decades
-
Emerging galleries to discover during Milan Design Week
Wallpaper’s Milan editor has the inside track on the younger design galleries coming to town
-
Buccellati brings the forest and Furry Animals to Milan Design Week
The jewellery and silverware maison falls back on tradition for its Milan showcase, presenting its now-emblematic collection of intricately crafted creatures