A sustainable extension transforms BakerBrown’s converted forge
BakerBrown Architects crafts a sustainable extension for a converted forge project in southern England
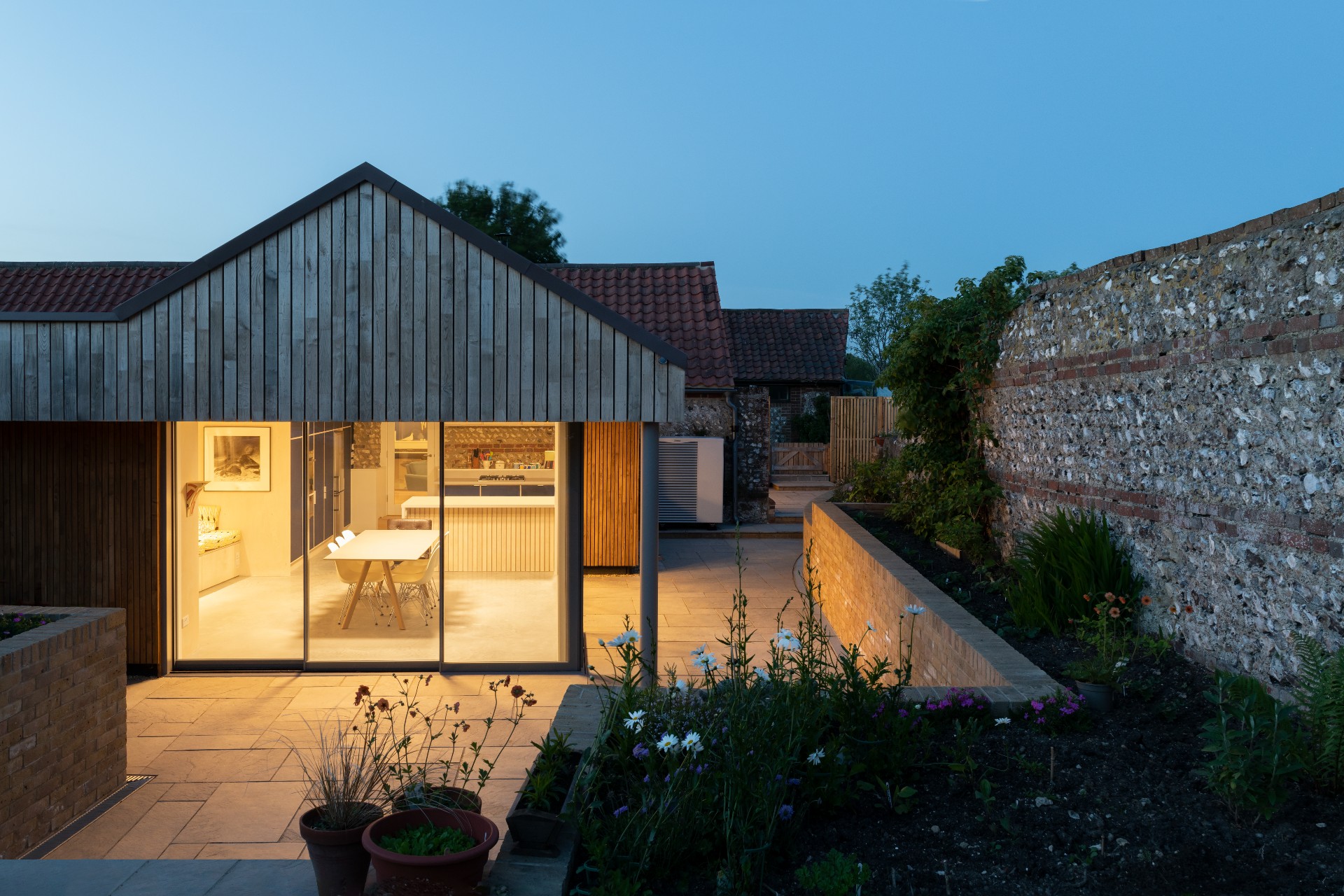
Ivan Jones - Photography
BakerBrown Architects has an award-winning reputation for sustainable architecture, pioneering ways of reducing a building’s footprint through meticulous design, careful use of resources, and thoroughly practical and attainable methods like insulation and the use of local materials and trades. In a similar vein, its latest work is a sustainable extension that makes the most of a unique site that brings together past, present and future.
The practice’s most recent project is a conversion of a long, low, gabled dwelling house in the south of England.
The original structure was once the village forge, making all manner of metal goods for local farmers and businesses. It was subsequently converted into a house and the surrounding neighbourhood upgraded to a Conservation Area.
The clients approached BakerBrown with the intention of creating a better relationship between the house and its garden, set at 90 degrees to the original structure.
The architects also had to upgrade the original masonry building. Built in the era between insulation and proper damp-proofing, it was becoming uneconomical to run.
The primary change is the creation of an extension that reaches out into the walled garden, transforming what was a modest sunroom into a large open-plan kitchen and dining room. A new red zinc pitched roof oversails the extension, providing solar shading for the glazing.
The main building has been overclad to radically improve its ability to retain heat in the winter and cool air in the summer.
Receive our daily digest of inspiration, escapism and design stories from around the world direct to your inbox.
Outside, a new rainscreen has been made from locally sourced sweet chestnut, adding to the increased thermal performance of the building.
The original boiler was replaced with a heat pump; despite increasing the floor area by around 40 per cent, the combination of more efficient heat generation and better insulation has reduced the property’s energy consumption.
All the design details are carefully considered with energy-saving in mind. The polished concrete floor slab in the extension acts as a heat sink, drawing in warmth from the glazing in winter. Sustainable birch plywood is used for the kitchen, ceilings, and joinery, lightly oiled to reflect light, while traditional vernacular elements like the original flint wall are retained and exposed.
Set up by Duncan Baker-Brown in 1994, the studio is based in East Sussex, and frequently works with vernacular forms, existing buildings, and conversions. Past projects include The Waste House – made, as the name suggests, from waste materials; and The House That Kevin Built, prefabricated using 90 per cent bio-based materials and the UK’s first EPC A* rated home. In 2017, BakerBrown authored The Re-Use Atlas: A designer’s guide to the circular economy, a pioneering book looking at how architects can make better use of limited resources.
INFORMATION
Jonathan Bell has written for Wallpaper* magazine since 1999, covering everything from architecture and transport design to books, tech and graphic design. He is now the magazine’s Transport and Technology Editor. Jonathan has written and edited 15 books, including Concept Car Design, 21st Century House, and The New Modern House. He is also the host of Wallpaper’s first podcast.
-
Inspired by Robert Mapplethorpe, A/W 2025’s best menswear captures a ‘menacing elegance’
‘A menacing, seductive elegance,’ is how Anthony Vaccarello described his A/W 2025 menswear collection for Saint Laurent, capturing a mood that ran through the season. Here, as seen in Wallpaper’s September 2025 cover shoot and film, a series of looks that invite a sense of risk when dressing for the months ahead
-
Artists imbue the domestic with an unsettling unfamiliarity at Hauser & Wirth
Three artists – Koak, Ding Shilun and Cece Philips – bring an uncanny subversion to the domestic environment in Hauser & Wirth’s London exhibition
-
No guilt, only pleasures await at Singapore’s first all-villa resort
From late-evening scented baths to midnight snack attacks, daily indulgences come in abundance at the tropical Raffles Sentosa Singapore
-
15 years of Assemble, the community-driven British architecture collective
Rich in information and visuals, 'Assemble: Building Collective' is a new book celebrating the Turner Prize-winning architecture collective, its community-driven hits and its challenges
-
Meet Studio Knight Stokoe, the landscape architects guided by ‘resilience, regeneration and empathy’
Boutique and agile, Studio Knight Stokoe crafts elegant landscapes from its base in the southwest of England – including a revived brutalist garden
-
What are biomaterials? Everything you need to know about Mother Nature's building blocks
Could the cities of the future be grown from plants, bacteria and fungi? Architects explain
-
Tour this compact Kent coast jewel of a cabin with Studiomama
Jack Mama and Nina Tolstrup take us on a tour of their latest project – a small but perfectly formed Kent coast cabin in Seasalter, UK
-
Boutique London rental development celebrates European courtyard living
London design and development studio Wendover unveils its newest residential project, 20 Newcourt Street, comprising nine apartments; we toured with co-founder Gabriel Chipperfield
-
A refreshed Fulham house balances its history with a series of 21st-century interventions
A Fulham house project by Bureau de Change creates a 21st-century domestic haven through a series of contemporary interventions and a deep connection to the property's historical fabric
-
The Monthly Architecture Edit: Wallpaper’s favourite July houses
From geometric Japanese cottages to restored modernist masterpieces, these are the best residential projects to have crossed the architecture desk this month
-
Visiting an experimental UK home: welcome to Housestead
This experimental UK home, Housestead by Sanei + Hopkins, brings together architectural explorations and daily life in these architects’ own home