Inside Gucci ArtLab, the house’s vibrant hub for innovation and craft
Gucci’s high-tech training school and testing laboratory in Tuscany combines craft and science to shape the future of sustainable design
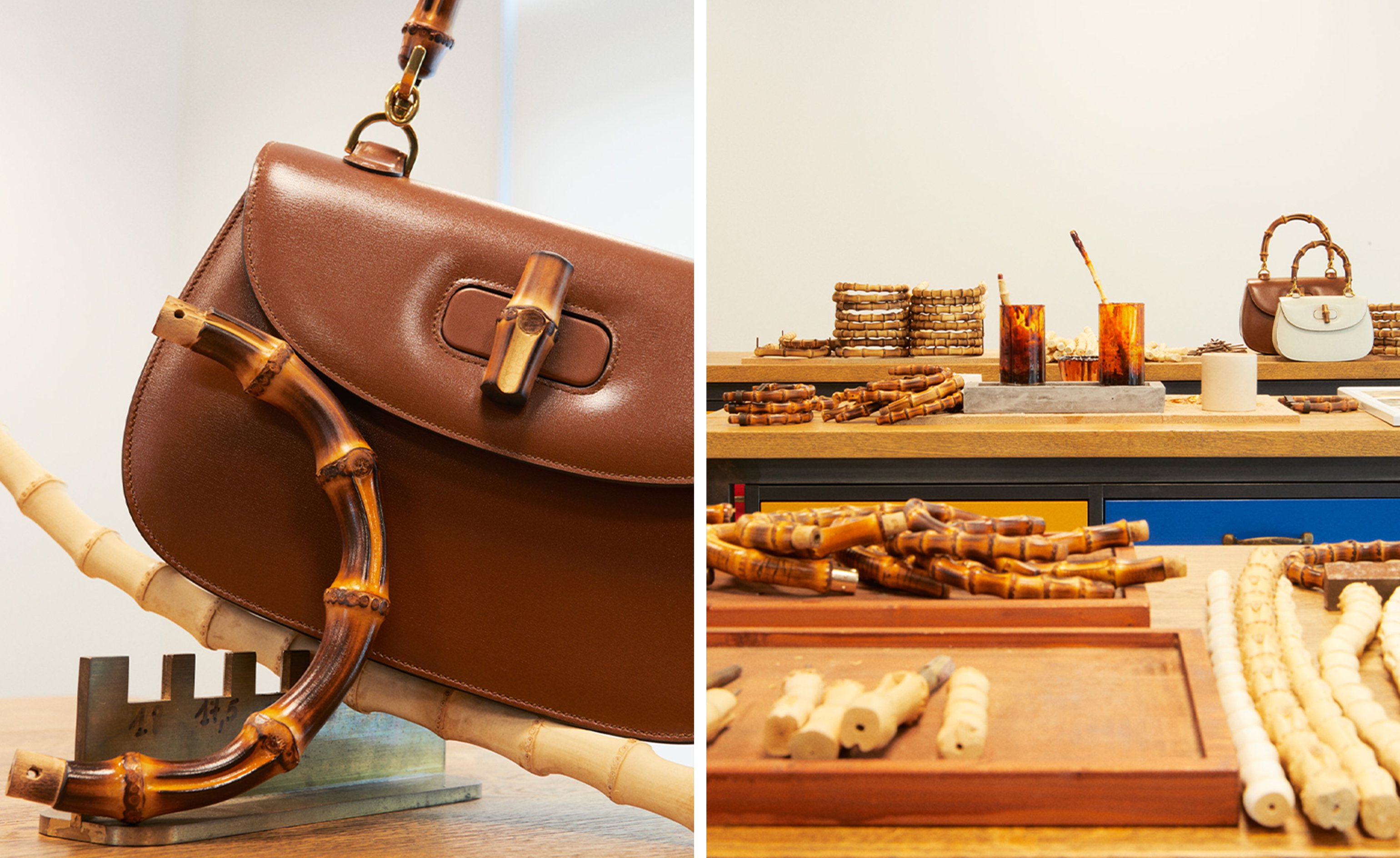
Paola Dossi - Photography
It’s a bright and sunny afternoon in Scandicci, a short 8km drive from the centre of Florence. Filled with FedEx vans, busy roundabouts and industrial warehouses, the bustling suburban hub stands in stark contrast with the Tuscan capital and its cultural landmarks, but for one conspicuous structure: Gucci ArtLab. With its vibrant 10m-high murals, the sprawling 37,000 sq m space is as unmissable as the statue of David – apt, given that a large-scale fashion anatomy is taking place.
Inside, artisan Fabio is adding volume to shoe lasts with putty before smoothing the surface by hand and checking how the light falls from every angle; Maurizio is finishing off a new-season diamanté loafer by joining its upper to its insole with precise hammer action; and Claudio is moving bamboo slowly over the naked flame of a Bunsen burner before bending it to achieve a perfect curved handle.
Inside Florence’s Gucci ArtLab
ArtLab’s archive library features hundreds of original moulds bearing the Gucci logo
Some date back to the time of founder Guccio Gucci, and finish under Tom Ford’s creative directorship
In adjacent laboratories, scientists and state-of-the-art robotics are working in tandem, testing soon-to-be cult bags for elastic-band fatigue and zip reliability. Treadmills are taking a pair of heels for a long-distance walk to calculate their durability, and a holdall is being checked for colour transfer using an automated mannequin that has been bopping on the spot, non-stop, for a couple of days.
An insatiable hive of activity, Gucci ArtLab is home to all of the Italian fashion house’s prototyping processes for its shoes and leather goods. Since its opening in 2018, manual and mechanical artisanship have been working hand in hand, with each of Gucci’s season-defining pieces engineered and fastidiously tested by a team of 950 specialists before hitting the catwalk.
Powered by photovoltaic panels and equipped with a system that limits unnecessary energy consumption, the LEED- certified ArtLab includes the classrooms and workshops of École de l’Amour, Gucci’s education programme
‘When I created ArtLab, my main thought was to give people the opportunity to be creative and express themselves,’ says its CEO Massimo Rigucci as he gives us a rare guided tour. ‘We’re not just creating a technical space, but [one filled with] emotions.’ ArtLab is a hub of shared skill sets and experience that speeds up innovation and short-circuits unnecessary waste. ‘We have 3D programmes that allow us to simulate an accessory rather than building a physical prototype and throwing the material away [afterwards],’ says Antonella Centra, EVP of general counsel, corporate affairs and sustainability. ‘But you can see it’s not replacing the human touch, it’s complementary.’
The brand’s ambition with ArtLab doesn’t stop there. Operating alongside its specialist research and development areas is the jewel in ArtLab’s crown, the École de l’Amour (‘School of Love’). Here, aspiring artisans can learn the skills of the trade from experienced maestros. It felt vital to Rigucci that students learn on the factory floor.
‘We’re trying to recreate the small artisanal workshops that I remember [growing up],’ he says. ‘I came from a factory where my mother taught us about shoes so that [the craft] would continue. This is something we want to do inside our organisation, too. They need to feel and touch the culture and the people who create it.’
Receive our daily digest of inspiration, escapism and design stories from around the world direct to your inbox.
A paper model of a ‘Jackie 1961’ shoulder bag
One of the white lab coats worn by teachers at Gucci’s École de l’Amour
On the day of our visit, Marco, who worked as a Gucci pattern maker for 40 years before becoming a full-time teacher at the school, is taking a group on a six-month placement through assembly steps. His colleague Matilde, an expert seamstress, is showing them how to stitch and sew. ‘It really keeps the passion alive, and they teach us so much, too,’ says Matilde.
Busting the myth that there is a lack of appetite for younger generations to pursue craftsmanship in Italy, the academy regularly has 200 applicants for ten coveted places on each of its courses. Since its inception, more than 1000 people have passed through its doors, many of whom have stayed on in full-time employment afterwards. Thanks to their intensive training, they hit the ground running.
All Gucci shoes and leather goods are prototyped at ArtLab, including versions of its iconic 1953 horsebit loafer
From interrogating the molecular make-up of materials to sharing specialist skill sets, circularity is the buzzword here. One of the ArtLab team’s proudest achievements is that it contributed to the creation of Demetra, a new animal-free material engineered from viscose, wood pulp and bio-based polyurethane, which stands out for its potential to be scaled up and become open source. ‘We first went to Silicon Valley, but the scalability and quality [of its bio-leathers] would never have reached our requirements, so Massimo said we should be the Silicon Valley of Italy,’ says Centra.
Sustainability is already a big item on Gucci’s agenda. The Kering-owned company is nearing the end of an ambitious ten-year plan that has seen the house achieve an overall traceability rate of 97 per cent for its raw materials to date. It’s a mindset that permeates not only the purpose of ArtLab and its artisans, but its LEED-certified space, too. Designed to inspire at every turn, its solar-powered white rooms are accented with joyful fuchsia boxes (‘I love it, it gives energy,’ enthuses Rigucci), while a dramatic red staircase was ‘designed as a portal through which our employees are transported into a world of creativity and craftsmanship’. Gucci ArtLab prizes innovation alongside preservation, and computing alongside craftspeople. ‘We’re creating a dream for the world, not just products,’ says Rigucci.
A version of this article features in the September 2023 Style Issue of Wallpaper*, on sale now available in print, on the Wallpaper* app on Apple iOS, and to subscribers of Apple News +. Subscribe to Wallpaper* today
Scarlett Conlon a freelance journalist and consultant specialising in fashion, design and lifestyle. Before relocating to Italy, she held roles as deputy fashion editor at The Guardian and Observer and news editor at British Vogue in London. She is currently a regular contributor Wallpaper* Magazine among other prominent international fashion and design titles.
-
Four under-the-radar travel destinations to book in 2026 – before everyone else does
You'd be forgiven if none of these locations are on your travel bingo card – yet
-
Estudio Ome on how the goal of its landscapes ‘is to provoke, even through a subtle detail, an experience’
The Mexico City-based practice explores landscape architecture in Mexico, France and beyond, seeking to unite ‘art and ecology’
-
Charlotte Chesnais brings her distinctive sensuality to sculptural new jewellery
Defined by curving shapes and luscious pearls, the jewellery designer's new collection, 'Joaillerie', has sculptural allure
-
Giant cats, Madonna wigs, pints of Guinness: seven objects that tell the story of fashion in 2024
These objects tell an unconventional story of style in 2024, a year when the ephemera that populated designers’ universes was as intriguing as the collections themselves
-
Fashionable Christmas baubles to accessorise this year’s tree, from Bottega Veneta to Loewe
Selected by the Wallpaper* style team, a gleaming array of Christmas baubles for fashion fans featuring fantastical designs from Bottega Veneta, Loewe, Prada and more
-
Gucci’s ‘Blondie’ bag revival sees the enduring 1970s accessory reimagined anew
First shown at Sabato De Sarno’s Gucci Cruise 2025 show in London, a new iteration of Gucci’s beloved ‘Blondie’ bag fuses 1970s insouciance with a crisp modernity
-
The breathtaking runway sets of S/S 2025, from beanbag animals to a twisted living room
Wallpaper* picks the best runway sets and show spaces of fashion month, which featured Bottega Veneta’s beanbag menagerie, opulence at Saint Laurent, and artist collaborations at Acne Studios and Burberry
-
The invitation for Gucci’s latest show was a reissued Enzo Mari design classic
Milan Fashion Week’s best invitation came from Gucci – a reissue of Enzo Mari’s ‘Timor’ perpetual calendar in the Italian house’s signature ‘Ancora’ oxblood red
-
The A/W 2024 menswear collections were defined by a ‘new flamboyance’
Sleek and streamlined ensembles imbued with a sense of performance take centre stage in ‘Quiet on Set’, a portfolio of the A/W 2024 menswear collections photographed by Matthieu Delbreuve
-
In fashion: the defining looks and trends of the A/W 2024 collections
We highlight the standout moments of the A/W 2024 season, from scrunched-up gloves and seductive leather ties to cocooning balaclavas and decadent feathers
-
In Tokyo, Gucci drafts local artisans to reimagine the Bamboo 1947 bag
Gucci’s ‘Then and Now’ exhibition in Tokyo celebrates 60 years of the Italian house’s presence in Japan. Here, local artisans tell Wallpaper* the story behind their contribution