Bespoke Partnership
These extraordinary materials make kitchens and bathrooms blissful
From tactile Volcanic Limestone bathtubs to fine fireclay sinks and exquisite brass taps and fixtures, matchless materials define House of Rohl and its collection of luxury brands
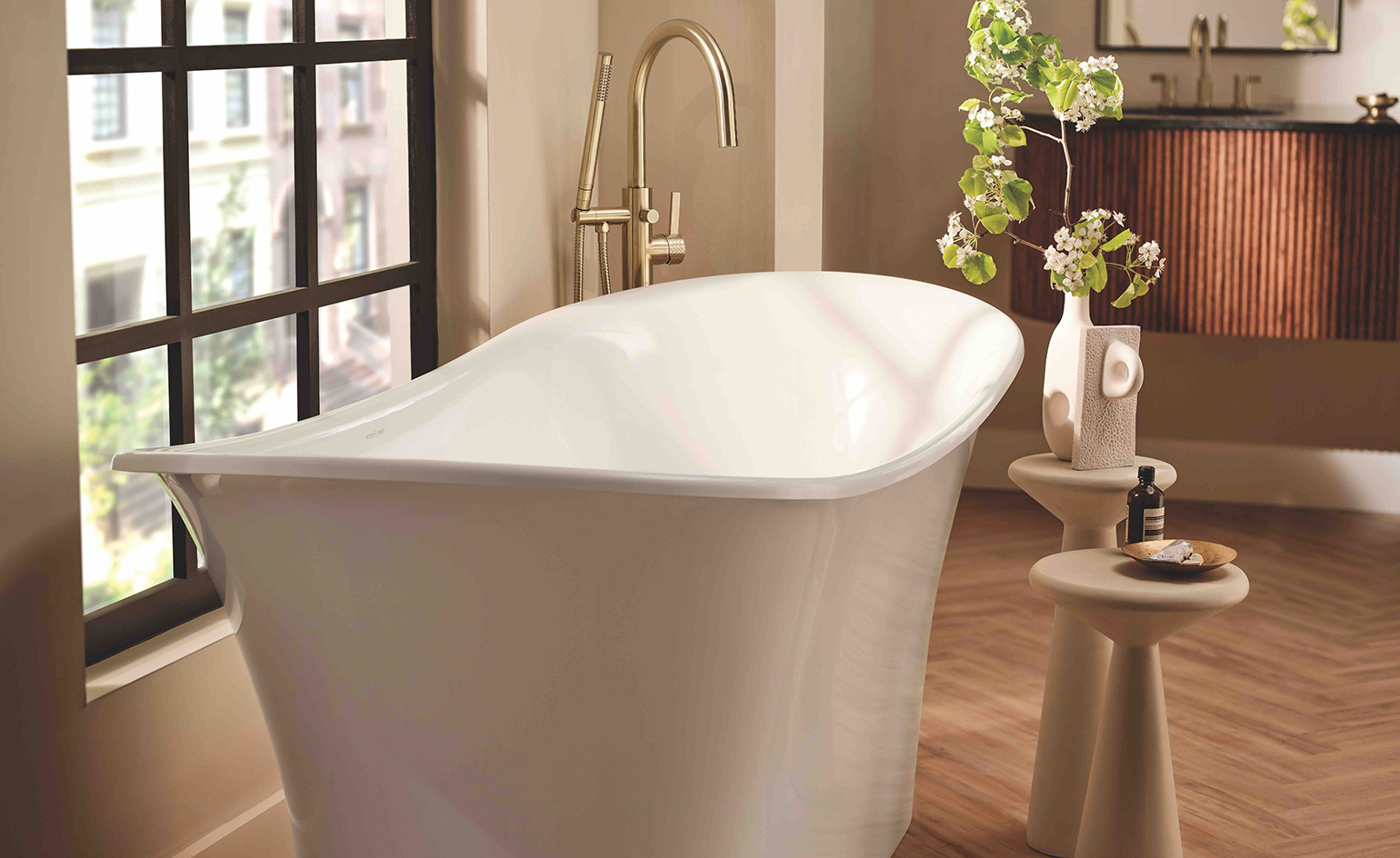
In partnership with House of Rohl
Cleansing, renewing and restoring, combining both the liquid delight of warm, falling water with the calming immovability of stone, ceramic and brass, contemporary kitchens and bathrooms offer a gamut of luxurious sensations: tactility and substance, alchemy and materiality. Such qualities are at the heart of House of Rohl and its collection of brands.
Victoria + Albert Volcanic Limestone baths and sinks
‘Amiata’ bathtub
Volcanic Limestone is at the core of House of Rohl bathroom materiality. The white rock is formed when immense heat and pressure from liquid magma transforms surrounding limestone. The result is a world-class stone of unrivalled strength and beauty, perfect for creating Victoria + Albert bathtubs.
Versatility, optimised insulation, liquid and heat retention are all vital considerations for bathroom materials. With each Victoria + Albert bathtub, cast from one single, hand-finished, stone-rich piece, a thinner wall construction and exceptional strength-to-weight ratio is guaranteed, the material offering superior strength and resistance to chips and cracks. No creaking or flexing of the bath ensures a quiet, unspoiled soak.
Colour is pure, consistent and naturally white. Exterior surfaces of each Victoria + Albert bathtub can be painted and personalised in a gloss or matte finish, and in a broad spectrum of colours to match or complement surrounding décor.
Shaws fireclay sinks
Top, precision craft at Shaws. Above, an artisan hand pours liquid clay into a porous mould
In a quiet, distinctly non-volcanic corner of north-west England the craftspeople at Shaws have been making sinks the same way, by hand, for over 100 years. Employing an age-old process passed down through generations, each Shaws sink is a work of art and the epitome of understated luxury.
Materiality is key to a Shaws sink’s construction, the clean lines and natural shapes of its designs formed using the time-honoured ‘slip casting’ method and locally sourced fireclay. The preferred process is manual and highly skilled; liquid clay is poured into porous moulds, glazed twice and fired for two days in specially designed kilns.
Shaws ‘Shaker’ sink in matte black
When the newly minted sinks are sufficiently dry, expert hand-finishing begins, through an artisanal procedure of sponging and ‘fettling’ to create a smooth surface. Only once a sink has been left to slowly dry out for a period of over 40 hours, is it deemed ready for a first coat of glaze. A second glaze is added to improve the feel and durability of the product. Each sink is then carefully fired in specially designed kilns at temperatures of over 1,200 degrees Celsius to complete the manufacture.
Perrin & Rowe brass taps and fixtures
A Perrin & Rowe tap in the workshop
To best convey water, efficiently and beautifully, from exterior source to expertly formed ceramic vessel, brass – cool and smooth to the touch – is the ideal material. At the Perrin & Rowe factory in the English Midlands, workshops are bound by a passion for traditional manufacturing craft that defines the brand.
Every product must be treated individually to ensure quality. Mass production has no business amongst its craftspeople who hand-forge brassware taps and sanitaryware from the highest quality brass. Perrin & Rowe’s manufacturing processes marry the latest technologies with hand-moulding and hand-polishing while surfaces are plated to a thickness that exceeds industry standards, ensuring a deep, protective coating that is resistant to wear and pleasing to the eye.
‘Brassware is also assembled by hand and each piece is individually water-tested,’ say the company founders. ‘Our casting plant in Wolverhampton is one of the last of its kind, carrying on a tradition that’s over a hundred years old. But what distinguishes us most is our high standard for performance and beauty. Because precision isn’t our method. It’s our mission.’
House of Rohl
Across its portfolio of brands, House of Rohl is unstinting in its pursuit of the best materials and outstanding artisanship and engineering. It sees the potential in stone and clay, brass and steel, poured and casted, glazed and fired, and transformed into the finest of products, bringing brilliance and beauty to kitchens and bathrooms.
INFORMATION
Receive our daily digest of inspiration, escapism and design stories from around the world direct to your inbox.
Simon Mills is a journalist, writer, editor, author and brand consultant who has worked with magazines, newspapers and contract publishing for more than 25 years. He is the Bespoke editor at Wallpaper* magazine.
-
Studio Urquiola’s immersive Kvadrat textile forest is inspired by the Nordic landscape
During Chart 2025, Studio Urquiola and Danish designers Tableau team up to present a textile installation showcasing Kvadrat’s nature-inspired new collection
-
The new Plaud Note Pro deploys AI to transform the spoken word into searchable data
The Note Pro promises full-on conversational AI, a pocketable device that can capture roundtable chats and correctly attribute speakers, thoughts and action points. Help or hindrance?
-
10 things not to miss at London Design Festival 2025
We bring you the best new installations, exhibitions and products to launch at London Design Festival 2025 (13–21 September)
-
This São Paulo apartment was designed for content creators, and it’s certainly camera ready
A renovation of this penthouse saw the kitchen relocated to the heart of the home to suit the purposes of a couple who run a culinary YouTube channel
-
Get back to basics with these low-fi and long-lived kitchen tools
Fed up with the perennial pairing and needy notifications from too many smart devices? Discard digital and go all-analogue with our essential selection of battery-free kitchen tools and accessories
-
Febal Casa’s ‘Onda’ kitchen island and sideboard with Zaha Hadid Architects ripple with possibility
Architectural fluidity and manufacturing excellence meet in a next-wave furniture collection
-
Tristan Auer and Axor redraw the bathroom as living space
‘Trust your taste and show it,’ says interior designer Tristan Auer as he reveals his concept for the ‘Distinctive’ bathroom campaign for Axor
-
Earthy new colour palette for VitrA’s Plural bathroom range
Designer Terri Pecora takes a deep dive into the cleansing, convivial effects of sage, terracotta and stone
-
Ceramica Cielo’s latest washbasin is inspired by the Bauhaus
Marcel is Ceramica Cielo's latest washbasin design, created by the brand's artistic directors Andrea Parisio and Giuseppe Pezzano
-
Tom Dixon’s bathroom designs for VitrA named Best Fluid Forms
Tom Dixon's ‘Liquid’ bathroom collection for Turkish brand VitrA wins Wallpaper* Design Award 2022
-
Possi’s modular kitchens work in every space
Danish brand Possi makes its debut with modular kitchens that bypass the limitations of traditional kitchen design